What Mechanisms Influence Powder Flow?
Powders consist of particles, typically combined with air, and often appreciable levels of moisture too. Powder flow occurs when its constituent particles move relative to one another.
Powder flow is influenced by particle properties, such as size, shape, surface roughness and charge, and by external variables, for example, aeration or consolidation of the sample, or the ingress of moisture. The flow properties of powders are industrially critical but complex, and not yet amenable to mathematical modelling.
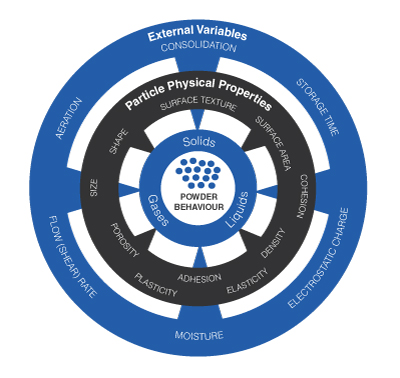
Figure 1 – Variables that influence powder flow
It’s a common misconception that powder behaviour can be described by just understanding its flowability, and equally that flowability is a discrete property that can be quantified with a single number. Unfortunately, neither of these assumptions are correct, which explains why a fundamental understanding of powder behaviour remains elusive. Consider a loosely packed powder in a glass jar and visualise its response when the jar is tumbled. Then consider how differently it would behave if the jar was first tapped several times on a hard surface. Differences in behaviour between the loosely packed state and the tapped, consolidated state would be due to the bulk characteristics of the powder. If the powder were dry sand, then it would behave in a similar way before and after tapping. However, if the powder were flour, for example, it would flow very differently after it had been tapped. A single flow parameter, or knowledge of physical properties such as particle size or shape alone, would not inform on this varying behaviour.
Learn more about powder flow
Why Measure Powder Flow?
Powders are integral to a huge range of industrial processes, contributing to an estimated 80% of all manufactured goods. Despite being commonplace throughout many applications, powders continue to present challenges during product development, manufacturing, and in quality assurance. Powders may be subjected to storage, transportation and handling, before and during processing. In storage, they can consolidate or cake and become more resistant to flow. When aerated, for example by discharge from a hopper, separation of the particles by air reduces resistance to flow. Typically, a consolidated powder can require around 100 times more energy to make it flow than the same powder aerated; for a fluidizable powder this may be more than 1000 times.
It is therefore essential to generate relevant data by testing powders under conditions that simulate the environment and specific stresses associated with a process or application.
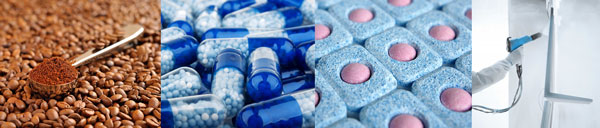
Figure 2 – Powders are used in a wide array of industrial processes, from food to spray coating
How to Measure Powder Flow?
Dynamic powder testing with a Powder Rheometer® directly quantifies powder flow properties across a broad range of stress regimes by measuring the energy associated with bulk powder movement. Powder rheology has seen considerable advances in the last decade and our understanding of how to test powders to support industrial processing and use has continued to progress. Studies can now be implemented effectively and precisely to derive valuable correlations for the optimisation of both process and product performance.
Learn more about powder flow testing solutions
Further Reading
Further information on powder flow and powder behaviour for different industries is also available via our applications pages - freemantech.co.uk/applications