Why is Powder Characterisation Important?
From pharmaceuticals, paints and coatings to metal components, catalysts and batteries, particles and powders underpin the performance of a vast array of everyday products. Manipulating the form and functionality of these industrially vital materials is essential for commercial success and relies on a sound understanding of their properties. Relevant and effective analytical solutions drive progress in every sector, from the earliest stages of development, through to QC and the consistent delivery of high-quality products.
Powders usually contain particles, liquid and air with powder properties, such as flow, influenced by a range of particle parameters, and 'system' variables such as degree of aeration (Figure 1). Analytical requirements for powder characterisation correspondingly extend from bulk powder measurements through to techniques to quantify internal particle structure.
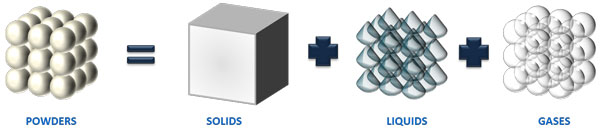
Figure 1 - Powders usually contain particles, liquid and air with powder properties, such as flow, influenced by a range of particle parameters, and 'system' variables such as degree of aeration.
Exploring industrial requirements for powder characterisation
A good starting point for an assessment of powder characterisation tools required for particles and powders is a clear understanding of the difference between the two. A particle is usefully described as a small portion of matter, this article is limited to the discussion of solid-phase particles.
Particles are individual entities with, for example, a defined size and shape. Powders, in contrast are more helpfully considered as bulk assemblies. They contain particles but also (most usually) air, and often moisture too. The properties of the particles that make up a powder directly affect its behaviour, a classic example being that finer particles are usually associated with poor flowability. However, so too do other ‘system’ variables, such as the degree of aeration or consolidation of the powder. Furthermore, though there are established links between particle properties and powder behaviour these are many and complex. It is not feasible, from current knowledge, to predict how particles with specific characteristics will behave as a powder.
The analytical toolkit for powders therefore extends from particle characterisation to bulk powder testing techniques. Particle characteristics are the levers manipulated to meet performance targets, but bulk powder properties often define many of these targets. Marrying the results from both types of analysis is often the key to fully evaluate powder characterisation.
Dynamic Powder Testing
What does it measure?
Dynamic powder testing enables quantification of the flowability of powders in a consolidated, moderate stress, aerated or even fluidised state via parameters including basic flowability energy (BFE) specific energy (SE) and aerated energy (AE).
In dynamic testing, flow properties are generated from measurements of the axial and rotational forces acting on a blade as it is precisely rotated through a powder sample (Figure 2). BFE, a baseline parameter, is measured with a downward traverse of the blade which pushes the powder against the confining base of the sample vessel. It quantifies confined or forced flow behaviour, in a low stress powder. An upward traverse, in contrast, measures SE, the unconfined flow properties that a powder exhibits when flowing under gravity in a low stress state, during gravitational filling for example.
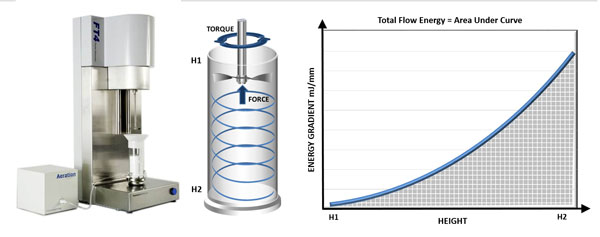
Figure 2 - Dynamic powder testing quantifies flowability and can be used to characterise powders in a consolidated, moderate stress, aerated or even fluidised state.
Dynamic testing enables direct assessment of the response to air, since measurements can be made while air is passed through the sample, at a known velocity, up to the point of fluidisation. Such measurements generate values of AE. The flexibility to tailor test conditions to simulate the process environment enables quantification of the impact of consolidation, flow (or strain) rate, and a range of other process-relevant variables.
Value added
Dynamic powder testing was developed specifically to measure powder flowability under conditions that directly simulate those encountered in routine powder processing. The technique generates data of direct relevance to a diverse range of unit operations including:
- Blending
- Die-filling
- Tableting
- Granulation
- Fluidised bed drying/reaction
- Volumetric feeding
- Hopper discharge
- Pneumatic conveying
Dynamic testing methods are well-defined, and instrumentation is highly automated giving the technique high repeatability and reproducibility, attributes that are lacking in many traditional powder characterisation methods. Dynamic testing is the most sensitive and differentiating bulk powder testing technique available and can differentiate samples that other techniques, including shear cell analysis classify as identical. This makes it a powerful tool from R&D through to QC.
The ability to directly quantify response to air is a particularly valuable attribute since even in processes where aeration is not intentional the entrainment and/or loss of air can transform powder flowability, directly impacting manufacturing efficiency.
Bulk Density and Compressibility Measurement
What is being measured?
Bulk density, as its name suggests, is a bulk powder property, based on measurement of a volume that incorporates the interstitial space between particles in a sample. Compressibility quantifies how that volume, and consequently bulk density, changes when a powder is subject to an applied stress.
Making measurements
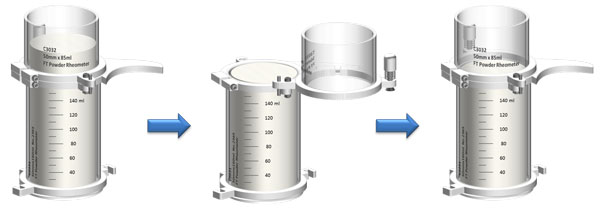
Figure 3 - Vessel splitting is an effective way of generating a precisely known powder volume and a level surface, for the accurate determination of bulk density.
Bulk density simply requires the accurate measurement of the volume taken up by a known mass of powder (Figure 3). However, it is important to recognise that because measurements of bulk density consider the interstitial space between particles, they are a function of factors that change that space. Such factors include direct consolidation, vibrational consolidation and changes to particle size and shape, since these can impact packing behaviour. Processing may leave the true density of particles unchanged but significantly alter bulk density and reproducible bulk density measurement relies on a defined sample preparation method. Compressibility is determined from measurements of density as a function of applied normal stress (Figure 4).
Figure 4 - Compressibility is determined by measuring how bulk density changes when a powder is subject to an applied normal stress and tends to be higher for more cohesive powders.
Value Added
Bulk density measured under controlled conditions is particularly informative for filling operations – die filling, for example, or packaging applications. These are often carried out on a volumetric basis, though the intent may be to achieve consistent mass. For this reason, bulk density often forms part of the specification for a powder product or raw material.
More broadly bulk density can be useful in highlighting changes in packing behaviour arising from variance in particle size, particle shape or other particle properties, or to elucidate differences in flow properties. Compressibility data is particularly helpful for elucidating how powders will perform when subject to consolidation/compression, during dosing operations, for example, in storage, and/or most notably in a tablet press.
Permeability Measurement
What is Being Measured?
The permeability of a powder bed is a measure of the ease with which gas can flow through it.
Making Measurements
Permeability is determined from measurements of the pressure drop across a powder bed when air is forced through it at a defined flow rate. Pressure drop is measured with respect to applied normal or axial pressure (Figure 5). As this pressure is increased the particles in the bed become more closely packed together and pressure drop increases. Darcy’s Law correlates permeability with air flow rate, bed height and pressure drop.
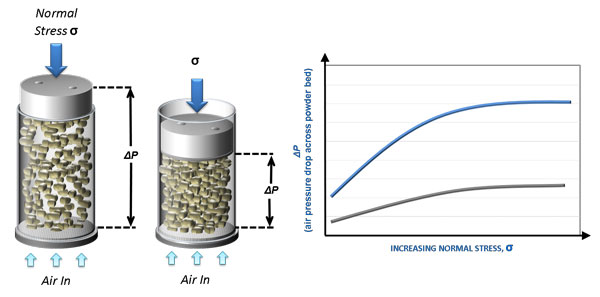
Figure 5 - Permeability is determined by measuring the pressure drop across a powder bed as air is forced through it at a defined flow rate.
Value Added
Permeability data are useful when trying to understand the effects of the many process environments in which powders can entrain or lose air. These include pneumatic and vacuum transfer, and storage in and flow from hoppers; low permeability is a known cause of low and or pulsing discharge flow. Permeability data are also of significant interest in processes such as vial filling and in dry powder inhaler formulation, where aerosolization of the dose is essential for efficient drug delivery.
Shear Cell Analysis
What is Being Measured?
Shear cell analysis can be used to rank the flowability of powders via metrics such as Unconfined Yield Strength (UYS) and Flow Function (FF). It can also be used to quantify the strength of interactions between a powder and a material of construction via metrics such as a wall friction angle, which is used routinely in hopper design calculations.
Making Measurements
In shear testing a sample is consolidated in a disc or annular shaped ring under a known load. The force required to shear one consolidated powder face relative to the other is then measured at a series of lower applied loads (Figure 6). These data are mathematically analysed via an extrapolation process to determine UYS and FF. Wall friction angle is determined from analogous measurements by shearing the powder against a potential material of construction.
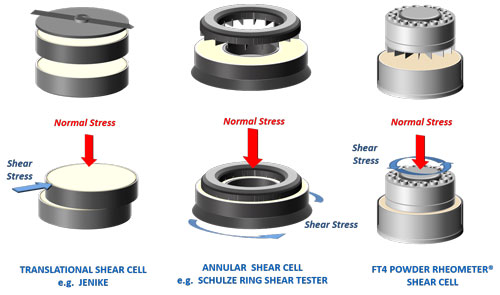
Figure 6 - Shear cell testers measure the forces required to shear one consolidated powder plane relative to another.
Value Added
The flowability of powders is often a critical determinant of their processing and product performance, and by extension their value. Precise and relevant measurements of powder flow properties are therefore extremely valuable. Shear testing was developed specifically to generate the data used for hopper design and remains valuable for this application. More broadly it is helpful for evaluating how powders will behave in a moderate to high stress environment, particularly when transitioning from the static to the dynamic state.
The technique offers more control over the experimental conditions applied during testing than other, simple USP methods, enabling more relevant powder assessment.
In Summary
Powders are multi-component bulk assemblies and as a result, they exhibit complex behaviour that cannot be predicted from particle properties alone. This complexity makes powders challenging to process and measure, but at the same time delivers an array of industrially useful behavioural properties. The behaviour a powder exhibits is a function of its inherent properties and the environment to which it is subjected. The processing environment is therefore an additional variable which must be considered when determining powder behaviour. Comprehensive powder characterisation identifies properties that are critical for a given application, helping to secure a successful process-powder combination. Making sure that a powder and process are compatible is essential for long term, efficient manufacture and high-quality product.